关于氧化锌挥发窑的特点和相关知识介绍
发布时间:2023/6/30 17:14:54 点击率: 来源:高铝砖厂家 作者:荣盛耐材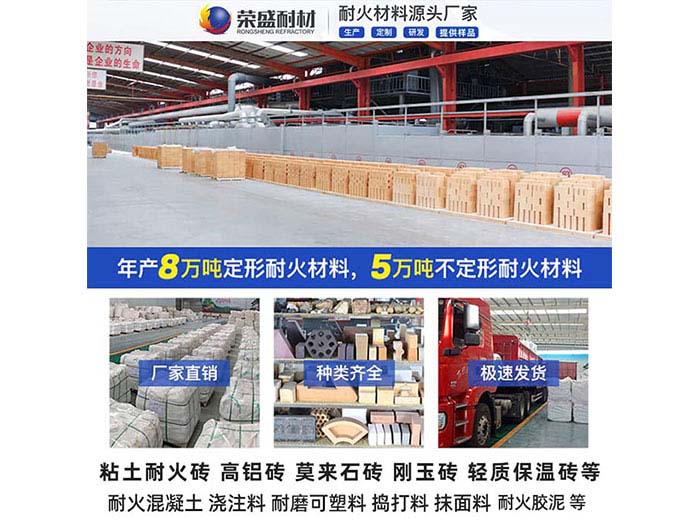
1.氧化锌挥发窑挥发的目的
湿法炼锌生产中所得的浸出渣含有较多的锌及其他有价金属(如铅、铜、镉、铟、锗及金、银等)。为充分利用资源,提高金属回收率并减轻其对环境的污染,故对浸出渣须进行处理,目前采用回转窑挥发的方法处理浸出渣。
2.氧化锌挥发窑用于对锌浸出渣的处理
挥发回转窑工艺在采用了新工艺、新设备,其特点是设备大、设备处理能力大、自动化程度高、产品质量较稳定,但总体投资大。系统除部分控制仪表外,全部采用国产设备。挥发窑系统中大量使用自动或半自动控制,在节约投资的前提下,大大减少了操作工劳动强度。整个系统是目前国内先进的挥发窑处理锌浸出渣系统。
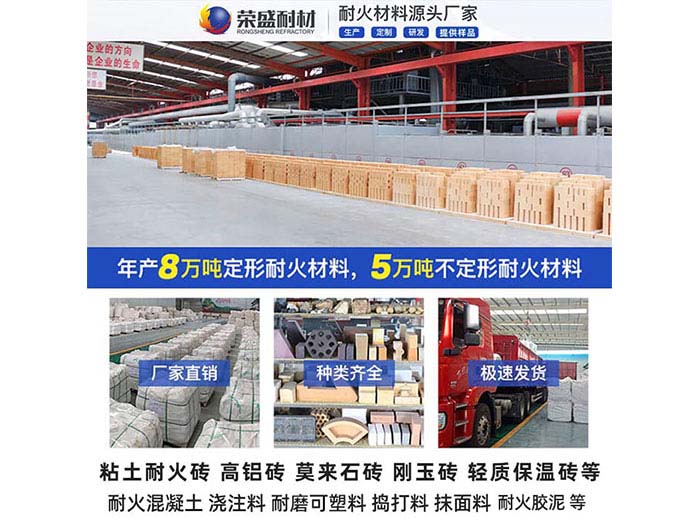
3.氧化锌挥发窑的结构部件
1.窑体:氧化锌回转窑的窑体一般由20毫米厚的钢板焊接(或铆按)成圆筒。
2.滚圈:滚圈并不直接套在窑体上,而是通过底座垫板安装在窑体上,其作用是加固氧化锌回转窑窑体,同时可以将筒体的重量传给托轮,在耐火材料生产中所使用的氧化锌回转窑,一般有5到8个滚圈。
3.托轮及托轮轴:托轮是通过热装法装在托轮轴上,而托轮轴则装在两个有青铜轴瓦的轴承内,轴承用水淖纵冷却后出来的水温不应超过25度。
4.挡轮:挡轮为一限制装置,限制氧化锌回转窑窑体在托轮上的位置,但它不能制止窝体的上下移动。
5.传动装置:氧化锌回转窑一般是利用齿轮来带动回转的。
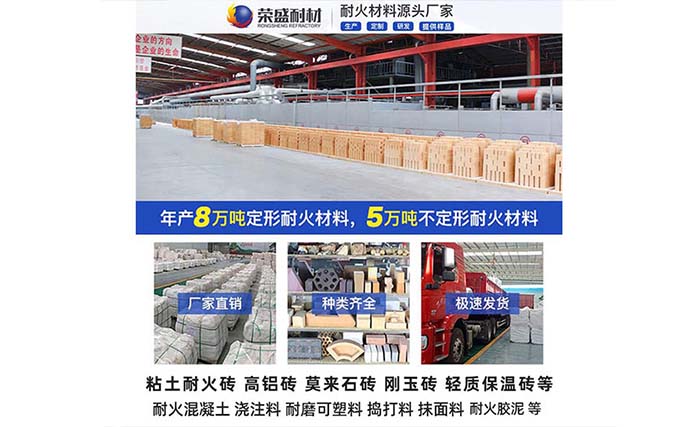
4、氧化锌挥发窑的组成系统
氧化锌挥发窑主要由:配料系统、上料系统、回转窑系统、渣水淬系统、氧化冷却系统、收尘装袋系统、烟气脱硫系统组成。
1. 配料系统主要目的是把含锌废料或锌矿粉与焦粉按比例配比并搅拌均匀,该系统由多仓称重配料机(选配)、皮带输送机和搅拌机组成;
2. 上料系统的目的是把搅拌好的混合料送入窑尾的料仓内,由输送机(胶带输送或斗式提升机)、料仓、给料机组成;
3. 氧化锌挥发窑系统是该生产线的核心设备,主要由筒体、耐火衬、传动机构、支撑机构、窑头罩、窑尾导料机构、风机、热源生成机构组成;
4. 渣水淬系统主要目的是把经高温煅烧锌蒸发后的高温废渣通过水急冷的方式激碎,该系统主要由冷水池、捞渣机、水泵、循环水池组成;
5. 氧化冷却系统主要目的是把高温的锌蒸汽充分氧化反应生成氧化锌并把气流降到合适温度,该系统由人字管、管道、配风阀、收集箱组成;
6. 收尘装袋系统主要目的是把生成的氧化锌成品从气流中分离出来并收集装袋,该系统由管道、脉冲除尘器、空压机、风机、卸料阀、称量包装机构组成;
7. 烟气脱硫系统目的是把煅烧过程中产生的二氧化硫进行脱除,达到达标排放;该系统主要由脱硫塔、反应池、再生池、曝气机、板框压滤机、耐腐蚀泵、风机组成。
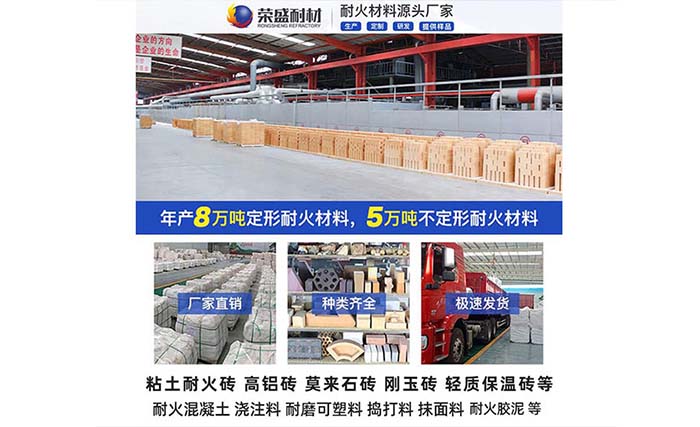
5、氧化锌挥发窑工作原理
氧化锌挥发窑工作原理就是利用金属锌、镉、铅和镉的硫化物以及铅的氧化物在高温下具有较高的蒸气压的特点,使锌、铅、镉等金属以氧化物形态转变为挥发物,铜和贵金属转入窑渣,再用另外的方渣从挥发物和窑渣小回收这些金属。一般多采用氧化锌回转窑处理含锌的滤饼。滤饼中的锌主要以铁酸锌、氧化物和硫酸盐形态存在,在氧化锌回转窑的高温下,铁酸锌和固体碳作用,还原为金属锌,同时锌、铅、镉的硫酸盐也被还原,井以硫化物和金屈形态挥发出来。从固相中还原和挥发出来的金属,在窑气氛作用下,又重新氧化,后主要以氧化物形态产出。
注意:送入氧化锌回转窑中的空气量,应确保密中烟气有足够的氧量,使之能再氧化早先已被还原出的全部金属蒸气、硫化物和一氧化碳。增加氧化锌回转窑的空气量,则会使还原区向进科端延长。相反,减少空气量,则还原区缩短,还原区起始段向排料端延伸。

6、氧化锌挥发窑的处理量
为提高低品位锌矿焙烧的生产效益,在保持窑温和锌发挥率,设备运转负荷有承受能力的条件下,可实验逐步提高给料量,使之达到相应的较大处理量。45米窑试生产期间,每小时进混合料高达9吨,产生窑粘结现象时,可适当增加焦炭加入量,提高窑内燃烧温度,改善窑料透气性并将粘结物熔化脱离窑壁,再恢复正常炉料。高温带窑衬腐蚀过快时,除加强该部位的窑体外部强制水冷却外,主要应控制适应于所处理锌矿脉石焙烧渣成份的合理挥发温度,使窑温略低于其软化点温度,又不影响锌的还原挥发率。此外,控制锌矿铅、硫含量,合理配矿,适当增加焙烧渣中氧化钙,氧化铝的含量,控制窑头鼓风量,不使高温带过于集中,也可缓解窑衬腐蚀速度,提高回转窑作业率。45米回转窑窑头高温带22米段砌筑高铝耐火砖,窑外为强制水冷窑体钢壳。为适应高硅氧化锌矿特点,高温带温度控制在1150-1200°C作业,窑内砌体可连续作业3个月以上。
7、氧化锌挥发窑从含锌烟道灰中制取次氧化锌的工艺
含锌废料和无烟煤粉(或焦粉)按一定比例兑料、搅拌成成分均匀的混合料,通过胶带运输或斗式提升机送至窑尾的混合料仓内,混合料仓下是园盘给料机,混合料通过园盘给料机计量后给料至回转窑内,随着回转窑的转动,混合料缓慢的从低温区向高温区运动,在高温区,混合料中的煤与窑尾鼓进的空气发生氧化反应,生成CO,CO和煤中的C与渣中的ZnO发生还原反应,生成Zn蒸汽,Zn蒸汽又被空气中的O2氧化,生成ZnO烟尘,在收尘器内被收集下来,剩余的渣在窑头水淬后进入渣池。
8、氧化锌挥发窑的结构及作用窑体
筒体由钢板焊制而成,窑头、窑尾设挡料圈,内衬窑砖。窑砖有三种:镁铝铬砖、高铝砖、粘土砖 支撑装置:托圈、托轮 传动装置:大齿圈、小齿轮、万向连接器、减速器、电机 窑头罩:烘窑装置(油枪)、窑头密封装置、排料装置等 窑尾沉降室:窑尾密封、下料管、沉降室 附属设施:液压站、润滑站 。
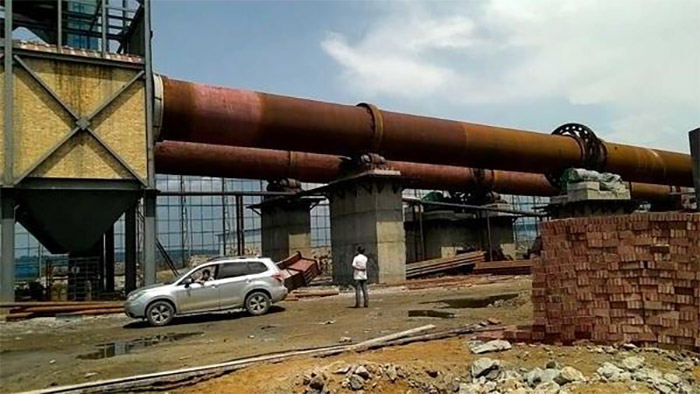
9、 氧化锌挥发窑的主要操作与控制
回转窑操作达到什么效果金属挥发率高:锌、铅、镉、铟、锗等 窑渣含锌、铟等有价金属低、含碳低 氧化锌质量好:金属含量高:锌、铅、铟等;杂质低:碳、铁、硅等 窑砖寿命长 成本低:各种消耗低(煤耗) 处理量尽可能大。
1.窑温控制 窑内温度越高,铅、锌氧化物的还原速度越快,挥发越完全。但温度过高,对窑衬腐蚀加剧,大大缩短窑衬寿命,并可能产生炉料熔化,形成炉结,恶化操作,降低金属回收率。因此,应根据炉料的熔点及性质控制适宜的温度。窑内温度沿窑长方向可分为四个温度带,即干燥带、预热带、反应带和冷却带。其中反应带长,温度高。一般反应温度为1100~1300℃,窑尾烟气温度为650~750℃。
2、窑内负压控制 窑内负压一般控制在-20~50Pa,负压过大进入窑内的空气多,反应带后移,窑尾温度升高,进料溜子易损坏,甚至有细颗粒进入烟道影响氧化锌质量。负压过小,窑内空气量不足,反应带前移,窑渣含锌偏高,甚至窑头有可能出现冒火现象。
3、强制鼓风 强制鼓风是改善窑况的主要因素之一,它可使窑温均匀,反应带延长,并使炉料适当翻动,加速反应过程。生产实际表明,强制鼓风可提高生产能力10~25%,铅、锌回收率分别提高4~5%及2~3%。强制鼓风压力一般为0.1~0.2MPa。
4、窑身转动窑身的转速对于炉料在窑内停留时间,反应速度及反应的完成程度有很大影响。转速太大,炉料在窑内停留时间短,虽然翻动良好,但反应不完全,渣含锌升高。转速太慢,炉料在窑内停留时间长,焦粉(无烟煤)燃烧完全,但处理量低。一般来说,炉料在窑内的停留时间为2~3h,窑身转速在60~120s/r。
10、氧化锌挥发窑开、停机操作
1、开窑操作
1)往窑内搬进适量柴火.
2)开窑点火前检查好各设备正常运行的准备工作,把直升烟道打开。3)插入油枪、鼓风管,开启油泵,明火点燃,开始烤窑升温。
3)烤窑升温时,严格执行升温计划,不可过急增、减油量,以防耐火砖炸裂,烤窑时及时调整油量和风量,使直升烟道冒白烟为好。
4)温度低于300℃(窑尾温度),间断转窑,每半小时转窑四分之一,温度达300℃以上,连续转窑。
5)当窑尾温度达600℃左右,即可进料。
6)进料时,行进8~10t焦粉帮助提温,然后再进混合料。进料初期,焦比要适当高些。待物料至窑头时,逐渐减少油量,待窑尾温度稳定在650℃左右方可停油,可通知开排风机,开钟罩阀,进行强制鼓风,关直升烟道,转入正常生产。
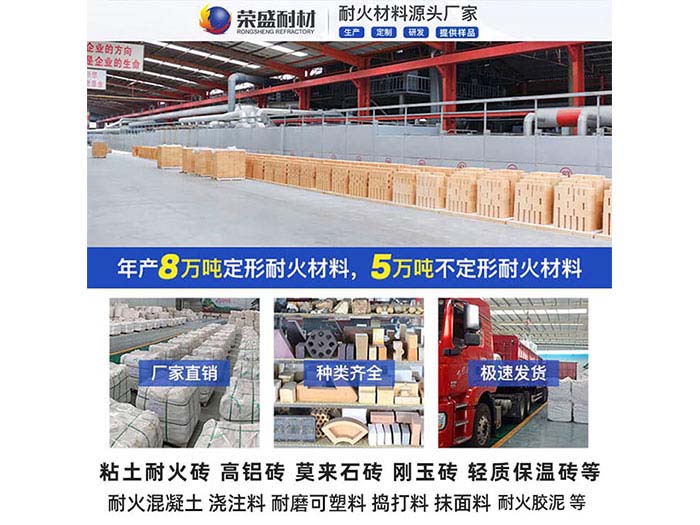
2、停窑操作
1)停窑前,先要把料仓内的料全部进完,待窑内物料中的锌基本挥发完后,再抽出风管,关钟罩阀,停止收尘。将窑密封起来,让其自然冷却,以防窑内衬砖炸裂
2)停料后,在窑内没有冷却下来之前,须继续转窑,当窑尾温度降到100℃以下,方可停窑。
- 上一篇:有耐2000度高温的耐火材料吗?
- 下一篇:没有资料